The Challenges
By and Large most exigent project to handle! Those who are working on it and modifying their design every day for better result or those who have worked in this and scrap it can understand the effort invested in it. It’s like Hurdle race, which never finishes.
Diesel fumes, high surrounding temperature, Diesel overflow, generator vibration, nonregulated battery supply, non‐uniform mounting holes, changeable generator depth, slanted DG surfaces, different DG shape, I can go on and on and these setbacks, which are due to surrounding, but I can’t help myself; have to introduce the biggest factor failure cause!!!!!! ! Yes! Yes! You are right! Human intervention! Those tempering! Theft! Connection lost! Not so proper mounting!
Including all the stumbling block, fuel level monitoring will never be as simple as monitoring the fuel level and sending it to customize location.
The Solution
No! We didn’t perform miracle! But yes, we have overcome these problems by learning from our experiences, used brand new technology and applied good old common sense.
Powertech has created a fuel sensor, which digitally senses the fuel level as the level increases or decreases. Its accuracy level is high due to change in fuel level causes change in count of sensor. These counters are enclosed in noncorrosive pole and they are dipped in the Diesel tank. Noncorrosive pole helps in weather proofing, prevents the wear‐and‐tear of sensor.
Due to temperature inside Diesel tank is lower than outer area, the performance of sensor become double fold. Sensor’s shape makes it easier to mount. Its different design helps in reducing human error and attempt of tempering reduces as well. Mounting seal assist in reorganization any attempt of damaging the sensor or theft. Inbuilt regulate power supply will provide the constant power supply to system, which minimize the chances of fluctuation in reading.
Fuel level sensor can give depth and volume of generator’s diesel tank, you can feed area and depth as per your specification and the fuel sensor will show the volume of diesel in generator tank. Max height of fuel sensor is customized with fuel tank depth but the area and volume of Fuel level sensor is user specific.
Graph of Fuel level with DG Run hours per day
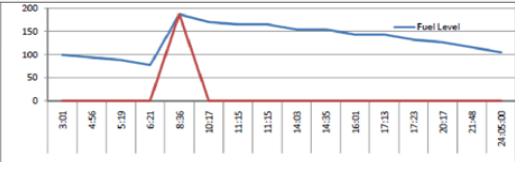
Above is a very small example of Fuel level sensor ( installed on a live site) per day reading with DG Run reading, the fuel level is decreasing with DG Run hour increasing, the fuel Top up shows the filling of fuel in diesel tank that day (i.e. 8th Oct)
Club this Fuel level sensor with any master device which have RS232 or Modbus communication protocol, and check the data, You can see the per day fuel consumption, Fuel top up, Fuel Drain etc.
With an add‐on Fuel Display unit, one can see the fuel depth, volume. User can set the fuel volume, area and Depth. Its low fuel level alarm is also settable at any fuel level; as per user’s specification; also as the low fuel alarm occur it will automatically gives a digital output.
Fuel level sensor enables us to avoid situation like Site being down due to DG couldn’t run! Fuel was low! With Continuous Fuel level sensing, you will have enough time to refill and avoid being in that type of putdown condition. Fuel consumption can be monitored with its change in level with DG run, Also the fuel theft can be stopped at some extend. With Fuel level monitoring you will have proper accounting of fuel refill, fuel consumption and DG set performance. You will also have got to know about that extra amount of Fuel getting disappear everyday without any accounting
The Benefits
- Timely Information of Top up & drain.
- Daily fuel consumption analysis.
- Fuel theft can be ceased.
- It also helps to avoid situations like site down due to low fuel in DG.